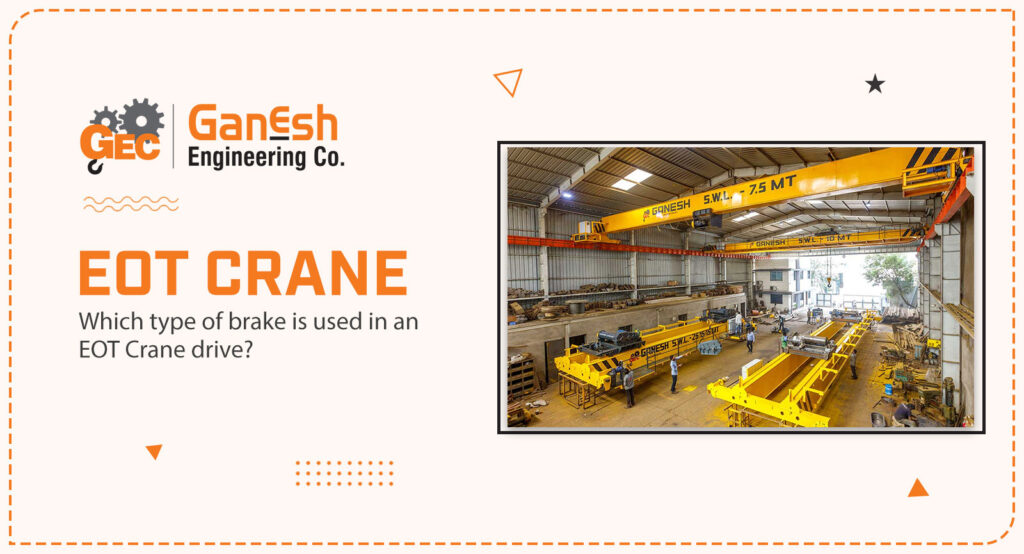
Electrical Overhead Traveling Cranes (EOT cranes) are the workhorses of countless industries, responsible for efficiently lifting and transporting heavy loads. Safety is paramount when dealing with such immense machinery, and a crucial component for ensuring safe operation is the crane brake system. But with various brake types available, understanding which one is used in an electrical overhead traveling crane drive can be confusing.
In this blog, we’ll discuss electrical overhead traveling crane brakes, exploring the different types commonly employed and their functionalities. We’ll also discuss how to choose EOT crane brake types.
The Essential Role of EOT Crane Brakes
Crane brakes serve two primary functions:
Controlled Braking: This allows for smooth and precise stopping of the crane during operation. The operator controls the braking force, enabling them to position the load accurately.
Emergency Braking: This critical function brings the crane to an immediate halt in case of a power failure, malfunction, or other emergency situation. It prevents uncontrolled movement of the load, safeguarding personnel and equipment.
There are two main categories of EOT crane brakes: service brakes and holding brakes.
Service Brakes for Controlled Stopping
Service brakes are engaged during normal crane operation to control the speed and positioning of the load. They are typically:
- Electromagnetic Disc Brakes: These brakes utilize an electromagnet to activate a disc-shaped rotor. When energized, the magnet attracts the rotor, creating friction that slows down the motor shaft. They offer fast response times and smooth operation, making them ideal for controlled braking.
- Thruster Brakes (Magnetic Drum Brakes): These brakes function similarly to electromagnetic disc brakes, but they use a drum-shaped rotor instead. They are known for their high holding power and are suitable for heavy-duty applications.
Holding Brakes for Secure Positioning
Holding brakes, also known as spring-applied brakes, come into play when the service brake is disengaged. They rely on a spring mechanism to keep the brake engaged, preventing the motor shaft from rotating. This ensures the load remains securely positioned even during power outages or when the operator is not actively controlling the crane. There are two main types of holding brakes used in EOT cranes:
- Disc Brakes: Similar to service disc brakes, these use a spring to press the brake pads against a disc, holding the shaft in place.
- Shoe Brakes: These brakes employ spring-loaded shoes that press against a drum, creating a frictional force that stops the shaft from rotating.
Selecting the Right EOT Crane Brake Types
The choice of crane brake types hinges on several factors, including:
- Crane Capacity: The brake system needs to be able to handle the maximum load the crane can lift.
- Duty Cycle: The frequency of use and the weight of typical loads will determine the required braking power and heat dissipation capabilities of the brakes.
- Lifting Speeds: Cranes with high lifting speeds require brakes with fast response times and the ability to handle rapid deceleration.
- Environmental Conditions: Cranes operating in extreme temperatures, dusty environments, or near water may require specialized brake types with appropriate corrosion resistance.
- Consulting with a qualified crane professional is vital to ensure you select the most suitable EOT crane brake types for your specific application.
Conclusion
Crane brakes play a critical role in ensuring these powerful machines’ safe and controlled operation. Understanding the different EOT crane brake types and their functionalities empowers you to make informed decisions regarding your crane’s braking system. By selecting the right brakes and maintaining them properly, you can contribute to a safe and productive work environment.